BATTERY-ELECTRIC 150-700 -SEAT AIRCRAFT DESIGN
TECHNOLOGY CHALLENGES
Analysis using data and methods from my ‘Whole Aircraft Design, So What …?’ (www.rawavcon.com) book explore the challenges of a battery- electric aircraft in the A320 or 737-8 class.
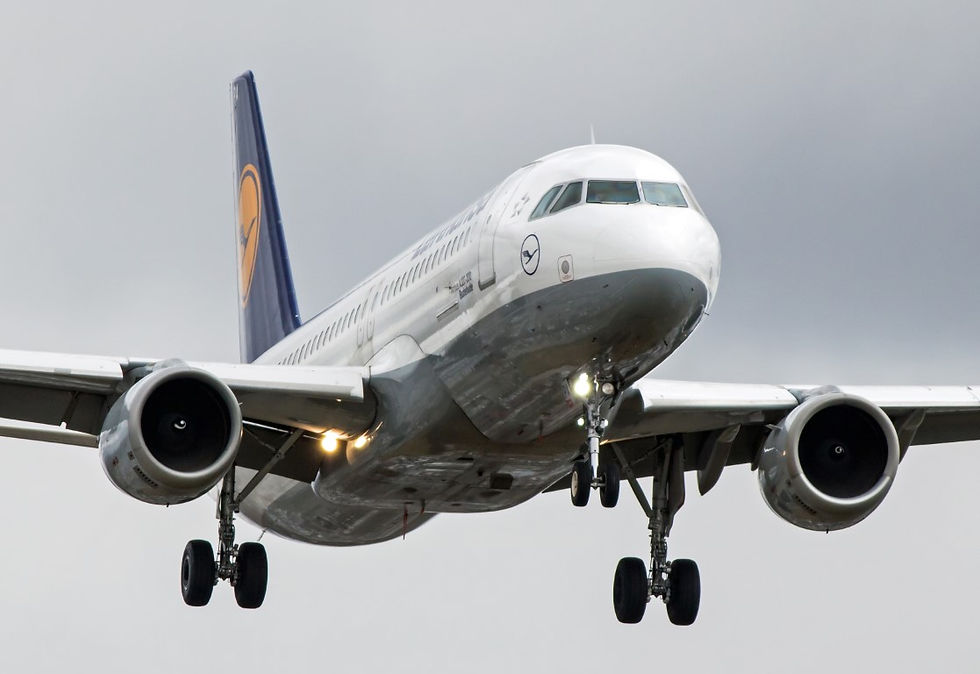
The process is very top-level, using Breguet Range calculations with the following fundamental inputs:
Empty Weight Fraction – the ratio of the aircraft empty weight to the MTOW where 55-60% has been a reasonable value for this class of aircraft smaller turboprops for a long time.re
Various feedback loops (to improving technology) and requirement evolution keep this ratio relatively constant. Although lower weight components reduce the empty weight, they also lower the MTOW at a constant design range. While the effect is smaller on the MTOW, improved aerodynamic and propulsion efficiencies primarily reduce the MTOW.
Finally, pushing the design range up increases the MTOW.
Generally, all these effects conspire to keep the empty weight fraction relatively constant with time.
Note: the following considers battery mass separate from the empty weight fraction
Optimum Aerodynamic Efficiency – the ratio of lift to drag at the design cruise conditions. Improving aerodynamic technology, structural technology, surface finish and configuration affect its value.
The configuration effect involves the aerodynamic efficiency increasing as the wing area represents an rising proportion of the aircraft’s overall wetted area, i.e. a growing proportion of the aircraft’s wetted area is generating lift and drag rather than only drag.
Propulsive Efficiency – This study considers this as the proportion of energy released from the energy storage system converts to propulsive power.
Specific Energy: Energy stored per kilogramme of fuel or battery
Other inputs:
Fuel Policy: The diversion distance and contingency fuel fraction. The 30-minute hold requirement is a constant.
Payload Mass: Design Mission payload
Design Range: Design mission flight distance
Lost Range: Net effect of losses incurred during taxi, take-off, climb, descent and landing, expressed as a design range increment.
STEP 1: BASELINE MODELLING
The successful modelling an aircraft representative of an A320 using appropriate inputs for the above parameters. This results proves the method’s validity.
STEP 2: BATTERY ELECTRIC AIRCRAFT
The very first action recognises that a battery-electric aircraft will never achieve the 3,500nm design range of the baseline aircraft.
Design Range = 600nm. This value should allow real world 500nm missions with wind and other operational effects included. Although a huge reduction from the baseline, it should cover the a substantial proportion of existing A320/737 usage.
Battery Tech Level = 800 Wh/kg installed pack level
This value should not be confused with the oft-quoted laboratory battery cell values. Introducing a cell into a pack adds considerable weight due to the packaging, power connectors and the power management systems.
Placing this pack on the aircraft will also likely require additional weight for safety systems or containment.
Hence, the value selected represents an extremely aggressive assumption for a 2030-2035 Entry Into Service (EIS). The now cancelled Eviation Alice claimed a 250Wh/kg battery pack for a 2023 EIS in its 2021 pre-flight test design. The battery details were never shared (at least I never saw them)
Propulsive Efficiency = 70% - representing a 75% improvement over the A320-class aircraft’s gas turbines. It is due to the considerably less losses converting the energy stored in the battery into propulsive energy
The batteries and motors will require considerable cooling, which ultimately causes increased drag. This must be included in the aerodynamic or propulsive efficiency values.
Fuel Policy – reserve fuel fraction NOT increased – it should be due to the battery-electric electric aircraft's constant mass through the mission.
ROUND 1 Results - The aircraft did not converge to a solution
MTOW reached >8,500t (10x more than an A380) and was still increasing exponentially after 17 iterations.
ROUND 2 Results – Converged! It remains a very heavy solution even with very aggressive Technology Improvements and Relaxed Fuel/Energy Policy
The resulting aircraft is ~65% heavier than the A320/737 with about 40 tonnes of battery carried and <20% of the range.
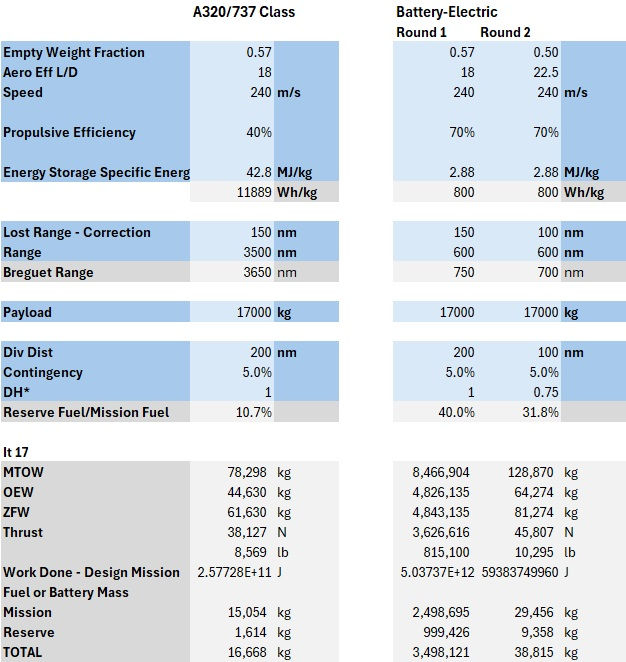
The 12.5% empty weight fraction improvement is very aggressive and therefore unlikely.
Carrying a 40t battery mass solely in the fuselage must increase the fuselage mass considerably as it more than doubles the baseline payload and cabin equipment/furnishing loads.
The wing mass should also increase as it no longer gains fuel bending relief.
Almost other components will scale up (get heavier) due to the higher MTOW and landing weights. The electric motors might be slightly lighter than the gas turbines they replace.
The 25% Aerodynamic efficiency improvement needs a Hybrid Wing Body to get close to the target. It probably requires considerable laminar flow, too. Note: it’s probable that the BWB configuration makes the empty weight fraction target even harder to achieve.
However, the larger wing relative to the fuselage (wetted aspect ratio) should provide a modest aerodynamic efficiency contribution.
CONCLUSION
Battery Electric airliners are very unlikely until battery technology accelerates will past the 1,000Wh/g at certifiable installed pack level, or there are huge improvements in aerodynamic and airframe weight efficiencies.
However, they might work better on smaller, slower sub-regional aircraft with shorter flight distances.
20000 nM Torque continiously +50% backup installed
Flight distance = infinite toilet required
No battery required
Power source mass is only 25 % of figures estimated by battery mass of 40 t
Do we need this aircraft design? Why not alternative or are we hell bent on A320
68000kWh daily
AC motors
email stt@mweb.co.za